Building an arcade table using an ODROID XU4 SBC (Single Board Computer) to run the emulation under Linux, I found the stock 40mm fan that came with the XU4 was just too annoyingly noisy.
I needed a solution which was not too tall because I was building this into an Ikea LACK side table so the available space was 54mm high. All the passive heatsink solutions I could find were too tall – the stock passive heatsink in the XU4Q was not enough to stop overheating on its own. I could still hear the buzzy 40mm case fan when enclosed in the table, I decided that I needed a simple, quieter solution which involved moving air and the existing heatsink.
As I also needed a case for the XU4, so I designed and 3D printed a case which would take a top mounted 80mm case fan. I’m using the eMMC to boot so there is a support for that. There are enough side holes for airflow, and to access the various XU4 ports. The XU4 is a snug fit, so much so that there is even a slot cut for the eMMC / SD Card selector switch which protrudes from the edge of the board. I have not found that I needed to screw the XU4 into the case, but that should be fine into one (or more I guess) of the corner quadrant pads.
Get the STL file from here: https://www.tinkercad.com/things/jQjhsvrBTEi
The case isn’t pretty, but it is functional and was designed to be hidden inside an Ikea table so it really didn’t need to be a diamond.
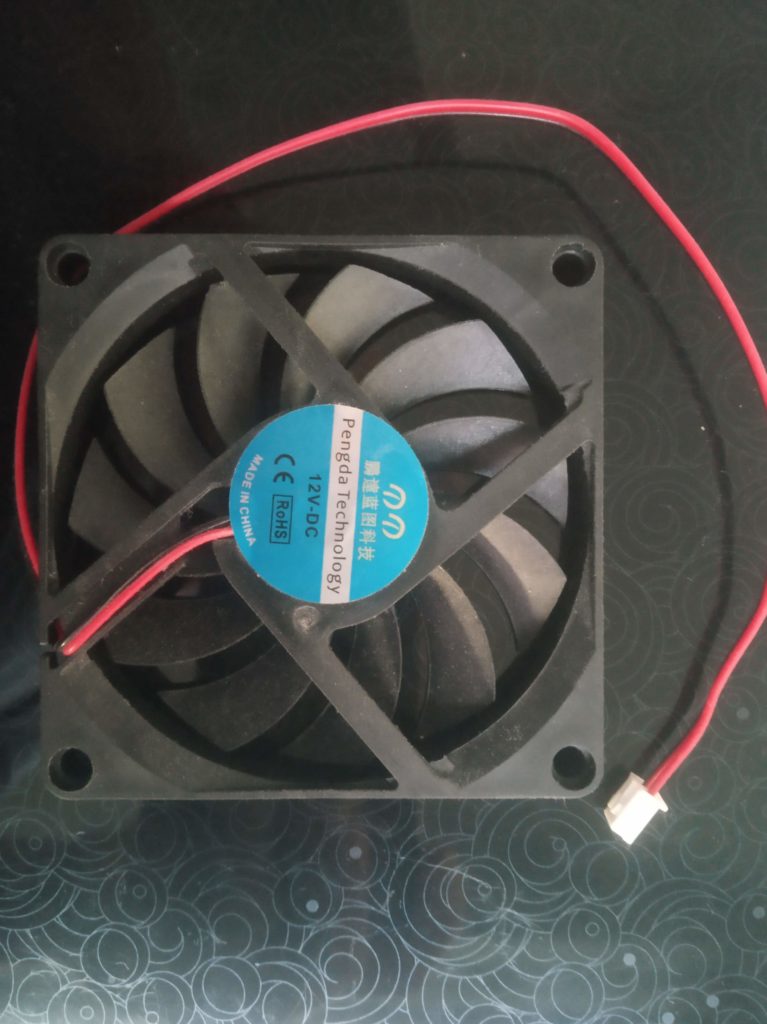
I sourced this 12V DC 2 pin case fan. Assuming the ebay link still exists, this one https://www.ebay.co.uk/itm/383664051536 which is 10mm high. I run this from the XU4, so at a maximum of 5V it runs slower than if run at 12V so quieter. Given that it moves more air than the stock 40mm fan, this seems to keep the board just as cool as the stock fan did, but significantly quieter.
This particular fan seems to be generic, there are lots on ebay / amazon which are similar. I was a bit worried it was going to be too noisy but it turned out to be pretty quiet, perhaps helped because it is being driven at 5V so spinning slower. Just a warning, some 12V fans may not work at 5V. Depending on your available space, you may be able to use a 15mm, 20mm or 25mm width fan. Having a larger area for the bearings, you may find that these fans can be made quieter, so you may be able to use a 5V 80mm case fan. If your fan has more than 2 wires, you should find that you only need to connect the positive and negative, the others can be left un-connected.
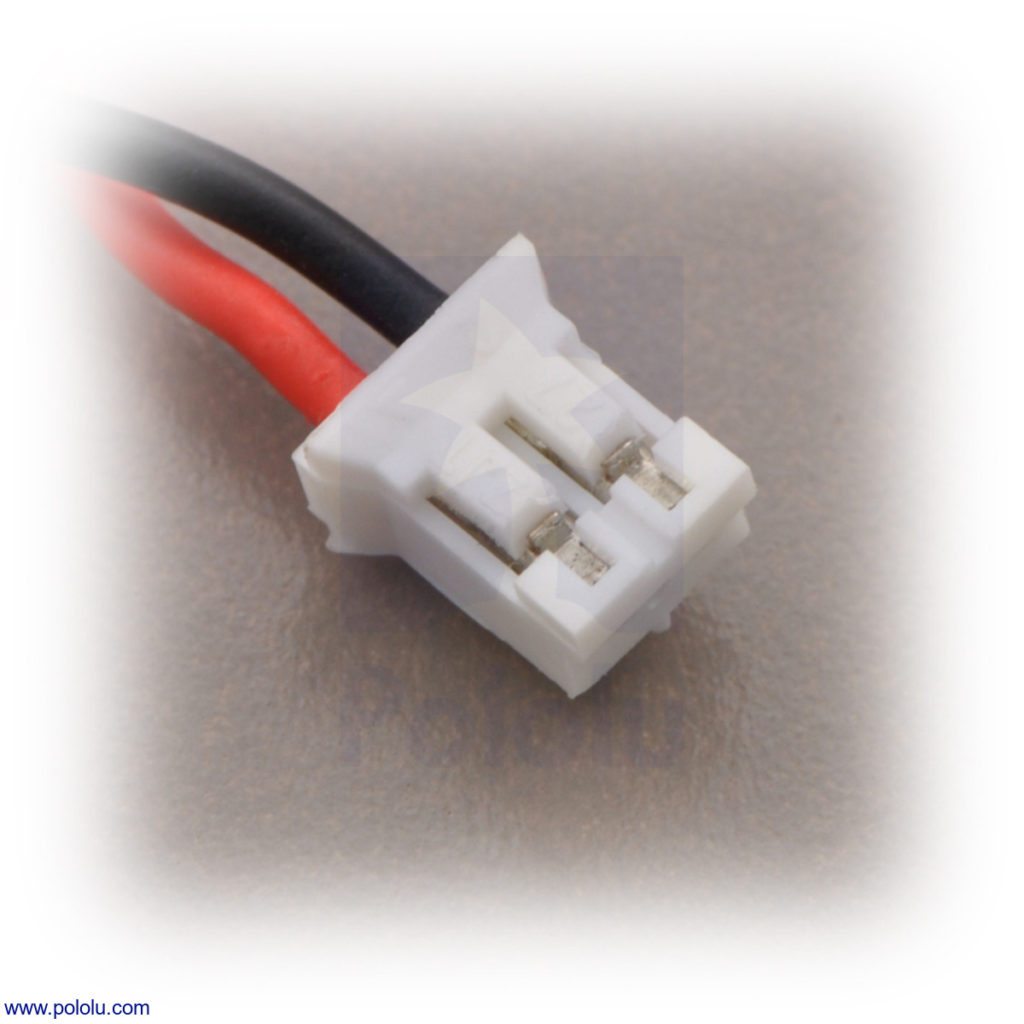
Like all case fans I’ve ever come across, this one comes with the wrong sized connector for an XU4 mother board, so I replaced the connector with this female 1.25mm pitch 2 pin JST connector. Again, assuming the link is still there, these ones: https://www.ebay.co.uk/itm/284270706948. This will require some soldering. Once connected, I screwed the fan to the lugs on the top of the case to keep it all secure.
I ran some prime95 tests and could not get the XU4 processor above 85 degrees C. In normal use, running the Naomi / Dreamcast emulator (lr-reicast) from Emulationstation / Retroarch, was probably about the most intensive and the core temperature hung around the 70-74 degrees C mark. This is also sharing a pretty small space with an Iiyama ProLite P1904S which has been dismantled but is still quite a warm beast.
If I did this again I think that I’d use the XU4Q model with the large passive heatsink, using this case / fan to contain and cool that, I think that it would fit ok but may need a shim or slight re-design to make the case walls higher.
I don’t have one but from what I’ve read, this should work on an XU3 without modification. For a Raspberry Pi you would need to do a little modification to the case design. On the Pi you would use dupont style female connectors with a 2.54mm pitch instead of the 1.25mm pitch 2 pin JST connector and connect the red wire to the +5V (GPIO 4) pin and the black one to Ground (GPIO 6) pin.
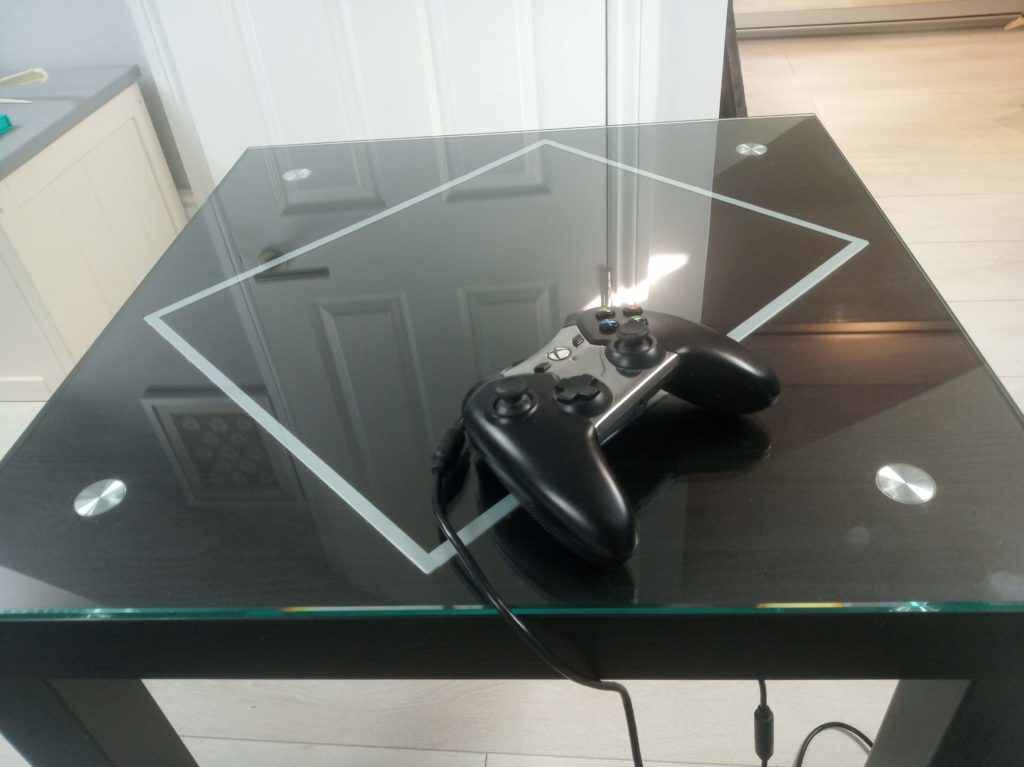
Here is the finished arcade table in case you are interested, we are very pleased with it all in all. I’ll write up how that was made when I get a chance.